Дешугаризація меляси в бурякоцукровій галузі США (частина 1)
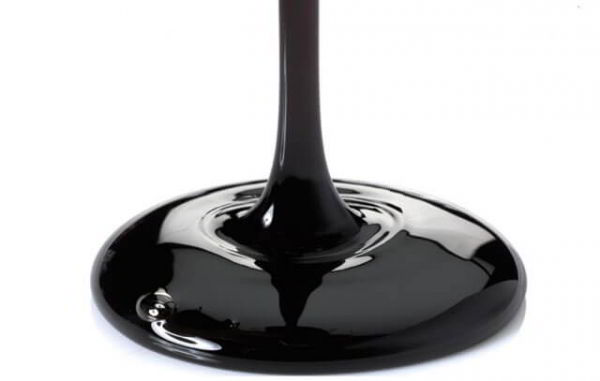
Дешугаризація меляси (MDS) — приклад широкомасштабного хроматографічного розділення, яке використовується у бурякоцукровій галузі США майже 40 років. Цей процес виявився економічно перспективним у сучасних ринкових умовах, а також у плані енергетичних витрат та екологічних наслідків. Як результат, більшість бурякоцукрових компаній США експлуатують одну або декілька установок MDS. Через різницю в ефективності та конфігурації існуючих установок іноді важко визначити бажані цілі розділення та визначити сфери оперативного вдосконалення. За останні декілька років хроматографічне розділення значно покращилося, і було розроблено нову конфігурацію обладнання. Спочатку розрахунковий вихід цукру ("білий цукор vs цукор у мелясі") 75-78% вважався цілком прийнятним рівнем. У сучасних системах цей показник збільшився до 88%. Однак в останніх літературних даних майже немає вказівок щодо того, як досягти цих результатів за різних технологічних конфігурацій. Дана стаття покликана дати відповідь на це запитання, а також допомогти в загальному розумінні широкомасштабних хроматографічних технологій, існуючих типів обладнання та факторів, які впливають на ефективність хроматографічного розділення. Протягом багатьох років системи MDS встановлювалися в автономному режимі, який можна було легко «включити» в роботу цукрового заводу звичайного типу (неавтоматизоване цукрове підприємство). Оскільки хроматографічний екстракт має суттєво інші характеристики, порівняно з сиропом, особливу увагу будемо приділяти способу впровадження переробки екстракту на цукрових заводах.
За матеріалами статті на тему «Дешугаризація меляси в цукровій галузі США — останнє оновлення» («Molasses Desugarization in the US Beet Sugar Industry — Recent Update») журналу «Міжнародний цукровий журнал» («International Sugar Journal»), вересень 2019 р.
Дешугаризація меляси (MDS) за допомогою хроматографії з псевдорухомим шаром (ПДШ-хроматографії) застосовується в бурякоцукровій галузі США з 1988 року, коли було встановлено першу комерційну систему на цукровому заводі Amalgamated Sugar в Твін-Фоллс, штат Айдахо. Хроматографічне розділення виявилося економічно ефективним методом вилучення сахарози з бурякової меляси, відповідно ця технологія отримала широке застосування в цукровій галузі. Сьогодні більшість бурякоцукрових компаній США використовують певний тип системи дешугаризації меляси.
Раніше технологія дешугаризації меляси (MDS) була заснована на періодичному процесі проведення розділення. У США перша система періодичної дії промислових масштабів була встановлена в 1973 році на цукровому заводі Юта-Айдахо, м. Мозес Лейк, Вашингтон. Однак використання періодичного розділення у бурякоцукровій галузі виявилося недовговічним і незабаром його було замінено технологією псевдорухомого шару (SMB). Безперервна технологія SMB потребує меншої кількості води та смоли для забезпечення аналогічного розділення, що помітно збільшує ефективність процесу. Незабаром у США процес SMB було адаптовано компаніями Amalgamated Sugar, lilinois Water Treatment та Applexion.
Спочатку системи дешугаризації меляси (MDS) використовувались лише для вилучення сахарози з нецукрів. Технологічна схема цього двокомпонентного розділення показана на Графіку 1. Кормова меляса розділяється на два потоки продукту: екстракт, багатий на сахарозу, який направляється в продуктове відділення для кристалізації, і рафінат, багатий на несахарозу.
Незабаром стало можливим багатокомпонентне розділення, що дозволило розділити мелясу на сахарозу, несахарозу та продукцію, багату на бетаїн. У 1989 році Finnsugar представив багатостадійний процес SMB, придатний для багатокомпонентного розділення, з використанням напівбезперервної операційної стратегії. Варіації багатостадійного SMB-процесу також були розроблені компаніями Mitsubishi, Organo та Applexion. У 1997 році Amalgamated Research (ARi) вперше представила зв’язану кільцеву хроматографію, де два сепаратори працювали послідовно один за одним, використовуючи приблизно таку ж кількість смоли та води, як і традиційний сепаратор. Це дозволило покращити виокремлення сахарози від нецукрів, а також вилучити очищений бетаїн із кормової меляси без витрат на додаткове використання смоли та води. На Графіку 2 зображено технологічну схему зв'язаної кільцевої системи дешугаризації. За допомогою першого кільцевого сепаратора кормова меляса розділяється на очищений бетаїн та модифіковану продукцію, багату на сахарозу. Модифікована продукція направляється у другий кільцевий сепаратор, де з рафінату видаляється більша частина залишкових нецукрів, щоб отримати екстракт високої чистоти.
Графік 1. Технологічна схема системи дешугаризації меляси (MDS) з виокремленням двох компонентів
Графік 2. Технологічна схема зв'язаної кільцевої системи дешугаризації меляси (MDS)
У застарілих системах дешугаризації (MDS) при ефективному режимі роботи установки з кормової меляси можна було вилучити 75-78% сахарози для виробництва білого цукру. Однак за останні роки планові виробничі показники сепараторів MDS помітно змінилися. Сучасні системи досягають набагато вищих показників чистоти та виділення, і тепер з меляси можна з легкістю вилучити 81-88% сахарози.
Перегляд наявної літератури з технології дешугаризації меляси (MDS) показує, що обговорення отриманих результатів можуть тривати по 20-30 років. Останні дані показують, що покращенню ефективності приділялося мало уваги, а правильні налаштування та аналізи, необхідні для досягнення цих результатів, майже не обговорювалися. Існує значна різниця між налаштуваннями існуючих систем MDS, тому нестача відкритих виробничих даних ускладнює порівняння різних технологічних конфігурацій. У даній статті підсумовано поточні досягнуті цілі розділення, пояснюються необхідні аналізи для досягнення та підтримання ефективної виробничої продуктивності, а також обговорюються варіанти введення системи MDS в роботу цукрового заводу.
Досягнення хроматографічного розділення
У бурякоцукровій галузі продуктивність хроматографічного сепаратора часто оцінюється шляхом визначення ступеня вилучення сахарози з меляси після кристалізації, тобто це обсяг білого цукру, отриманого з екстракту по відношенню до вмісту сахарози в кормовій мелясі. Amalgamated Research (ARi) позначає цей ступінь як Z-фактор, який розраховується за рівнянням (1), де R — вихід сахарози через сепаратор, E — чистота сахарози в екстракті, а M — чистота сахарози в отриманій мелясі після кристалізації екстракту.
Z-фактор був введений для об'єктивної кількісної оцінки продуктивності сепаратора за допомогою визначення відмінностей між різними поєднаннями ступенів чистоти та вилучення сахарози. Наприклад, у Таблиці 1 показано два варіанти можливої продуктивності сепаратора. З огляду на ступінь чистоти та вилучення сахарози окремо, складно визначити, який із цих двох варіантів кращий, але Z-фактор дозволяє легко їх порівняти. У розрахунках передбачається, що чистота кінцевої меляси становитиме 60%, а отже, Z-фактор називається Z60.
Таблиця 1. Порівняння двох варіантів продуктивності сепаратора
1 варіант | 2 варіант | |
Чистота сахарози в екстракті (%) | 90 | 92 |
Вихід сахарози (%) | 92 | 90 |
Вихід Z60 (%) | 76,7 | 78,3 |
Зауважте, що існує декілька комбінацій чистоти екстракту та вилучення сепаратора, які можуть привести до одного і того ж Z-фактору. Це свідчить про те, що в різних режимах роботи сепаратора можна отримати однакову кількість цукру.
Коли системи дешугаризації меляси (MDS) були вперше застосовані в бурякоцукровому виробництві, в режимі ефективної роботи можна було очікувати Z-фактор на рівні 75%. Однак в останні роки оновлені стратегії роботи покращили продуктивність сепараторів, що збільшило ефективність сучасних систем. Ступінь чистоти та вилучення сахарози збільшилися, а Z-фактор перевищив 80%. У Таблиці 2 вказані поточні очікування від сучасних сепараторних систем, припускаючи чистоту меляси на рівні 60% після переробки екстракту.
Досягнення в ефективності технології псевдорухомого шару (SMB) дозволили отримати задовільні результати з меншою кількістю смоли, зменшивши розмір та вартість систем дешугаризації меляси (MDS). Продуктивність хроматографічного сепаратора може бути представлена завантаженням, яке складається з поданого матеріалу, який переробляється за допомогою системи. ARi, як правило, виражає завантаження у фунтах нецукрів на кубічний фут смоли на добу.
Таблиця 2. Поточні цілі сепаратора
Чистота сахарози в екстракті (%) | 95,0 |
Вихід сахарози через сепаратор (%) | 91,0 |
Вихід Z60 (%) | 83,8 |
Графік 3. Збільшення засміченості нецукрами сепараторних систем ARi у розрізі тривалого періоду
При більшій засміченості нецукрами розмір системи можна зменшити, оскільки для забезпечення розділення потрібно менше смоли. ARi досліджував продуктивність сепараторів технології псевдорухомого шару (SMB) при різній засміченості нецукрами, і вдосконалення технологічних процесів дозволили збільшити завантаження, одночасно підвищивши продуктивність. Збільшення ефективності зменшило вимоги до смоли для комерційних систем та загальні капітальні витрати. На Графіку 3 показано, як завантаження систем ARi з часом зростало відносно базової лінії 100% завантаження у 1988 році. Зараз ARi працює з операційними системами до 800% завантаження від того, що використовувалося в застарілих системах, досягаючи при цьому кращих показників.
Ще одна розробка в процесі дешугаризації меляси (MDS) — це сепарація другого проходу, метод, рекомендований та розроблений ARi, для збільшення загального обсягу вилучення сахарози з кормової меляси. Після переробки екстракту в продуктовому відділенні, залишковий екстракт меляси містить значну кількість сахарози, яку неможливо було перетворити на білий цукор. Частину цього цукру можна вилучити шляхом переробки екстракту меляси назад у поданий до сепаратора матеріал; однак це, як правило, негативно впливає на показники SMB через накопичення нецукрів та зміну кольору. ARi виявив, що цього можна уникнути, зберігаючи екстракт меляси та переробляючи її через SMB окремо в процесі сепарації другого проходу. Це перешкоджає накопиченню осадів і дозволяє належним чином оптимізувати сепаратор для поданого матеріалу як першого, так і другого проходу.
У 2017 році хроматографію другого проходу випробували на промисловому випробуванні на цукровому заводі Amalgamated Sugar в м. Нампа, штат Айдахо. Приблизно 6 тис. т екстракту меляси було перероблено в установці дешугаризації (MDS), отримавши екстракт чистотою понад 90% та додаткові 2 550 т цукру після кристалізації. Після обох проходів загальний коефіцієнт вилучення Z-фактору склав 87,7%. Результати даного випробування наведені в Таблиці 3. Слід зазначити, що це випробування було відносно коротким і в ньому була використана стара система розділення; цілком імовірно, що з новішим обладнанням та більшим проміжком часу на його оптимізацію, продуктивність може значно покращитися.
Таблиця 3. Результати промислового випробування дослідження другого проходу
Чистота сахарози в екстракті меляси (%) | 66,9 |
Вихід сахарози через сепаратор (%) | 88,1 |
Вихід Z-фактору (%) | 87,7 |
Оптимізація сепаратора
Отримані результати підтверджують, що вихід цукру на рівні 88% цілком можна отримати на промисловому рівні. Однак для досягнення таких показників сепаратор повинен бути належним чином налаштований та стати єдиним цілим із цукровим заводом. Для цього потрібен регулярний контроль системи та точні аналітичні методи.
На показники роботи технології псевдорухомого шару (SMB) сильно впливають властивості поданого матеріалу, тому необхідний точний аналіз для відстеження будь-яких змін у якості сировини та екстракту. Багато заводів покладаються на видиму чистоту для вимірювання вмісту сахарози, але це не завжди є належним методом. У системах, які переробляють екстракт меляси за допомогою сепарації другого проходу, як правило, накопичуються нецукри, такі як рафіноза, оскільки їх важко видалити за допомогою хроматографії. Рафіноза може вільно обертатися, як сахароза, і її присутність впливає на показники поляриметрії та збільшує ступінь видимої чистоти. Різницю між істинною та видимою чистотою бурякової меляси за наявності рафінози показано на Графіку 4.
За допомогою визначення оптичного обертання рафінози можна скорегувати ступінь видимої чистоти для визначення впливу рафінози. Однак, навіть після врахування рафінози, між істинною та видимою чистотою часто залишається значна неузгодженість. Тому для точного спостереження за роботою сепаратора необхідно виміряти ступінь істинної чистоти сахарози за допомогою такого методу, як високоефективна рідинна хроматографія (HPLC) або ближня інфрачервона спектроскопія (NIRS).
Слід зазначити, що коли системи дешугаризації меляси (MDS) вперше були застосовані у бурякоцукровій галузі, ступінь видимої чистоти був стандартним методом аналізу, який застосовувався для визначення робочих характеристик сепаратора. У сучасних системах для встановлення цілей розділення використовується ступінь істинної чистоти. Оскільки ступінь видимої чистоти часто перевищує ступінь істинної чистоту на 2-6%, це вказує на ще більший розрив між цілями застарілої та сучасної моделі сепарації.
Налаштування установки дешугаризації меляси (MDS) також залежить від того, яким чином вона була інтегрована в роботу цукрового заводу. Вихід Z-фактору — це кількість цукру, виробленого з кормової меляси, і, як показано в рівнянні (1), залежить як від чистоти екстракту, так і від виділення сепаратора. Результатом цього зв'язку є те, що існує безліч комбінацій чистоти та виділення, які дають однаковий Z-фактор. На Графіку 5 показано чистоту екстракту та виділення сепаратора, які дають Z-фактор 75%, 80% та 85%, припускаючи, що чистота екстракту меляси становить 60%.
Спосіб переробки екстракту на заводі може впливати на належне поєднання виділення сепаратора та чистоти екстракту. Наприклад, виробництво екстракту високої чистоти може мати позитивний ефект, оскільки воно зменшує кількість нецукрів, вироблених у продуктовому відділенні; однак, якщо чистота екстракту занадто висока, то для досягнення повного екстрагування меляси необхідно провести більше трьох відварювань. На заводах з обмеженою ємністю продуктового відділення виділення сепаратора є важливішим, ніж чистота екстракту, оскільки екстракт високої чистоти не можна повність екстрагувати.
Графік 4. Різниця між ступенем видимої та істинної чистоти бурякової меляси за наявності рафінози
Графік 5. Поєднання виділення сепаратора та чистоти екстракту, які дають Z60 = 75%, 80% та 85%
Інтеграція переробки екстракту
Існують різні способи включення переробки екстракту в цілісну роботу цукрового заводу, а система дешугаризації меляси (MDS) повинна бути оптимізованою відповідно до її інтеграції. Оскільки екстракт зазвичай має вищу кольоровість, ніж сироп, його кристалізація за стандартною схемою трьох відварювань може бути проблематичною через сильну забарвленість виробленого цукру. Зміни процесу кристалізації, такі як четверте відварювання або змішування екстракту з сиропом у процесі переробки, необхідні для отримання високоякісного цукру. Тому розглянемо деякі схеми переробки екстракту, які використовувались у галузі бурякоцукрового виробництва, а теоретичний матеріальний баланс продуктового відділення буде використаний для розрахунку ступенів чистоти, виділення та кольоровості. Матеріальний баланс передбачає для кожного варіанту переробку 500 тис. т сиропу за 330 днів. У кожному варіанті визначається очікувана продуктивність сепаратора, а чистота екстракту та виділення використовуються як вхідні дані моделі.
Переробка екстракту одного проходу на заводах з одним продуктовим відділенням
У цій схемі кристалізації екстракт з установки MDS зберігається для переробки в продуктовому відділенні після завершення виробництва сиропу. Екстракт кристалізується окремо і не змішується з сиропом, а екстракт меляси не переробляється в процесі другого проходу. Ця схема кристалізації може бути реалізована з трьома або чотирма процесами відварювання. Через високу кольоровість екстракту, кондиційний цукор не можна виробити безпосередньо через вакуум-апарат, замість цього рекомендується подати екстракт до другого відварювання. Схема конфігурації трьох відварювань показана на Графіку 6.
Графік 6. Схема кристалізації з трьома відварюваннями для переробки екстракту одного проходу
Таблиця 4. Результати відтворення переробки екстракту одного проходу з одним продуктовим відділенням
Чостота комової меляси (%) | Чистота сепараційного екстракту (%) | Виділення сепаратора (%) | Вихід Z60 (%) | Чистота екстракту меляси (%) | Кольоровість білого цукру (IU) | Вихід цукру з сиропу (%) | |
Сироп | Екстракт | ||||||
60,2 | 93,0 | 92,0 | 81,6 | 72,2 | 20 | 30 | 97,6 |
У Таблиці 4 показані основні результати відтворення цієї схеми переробки екстракту. Чистота кормової меляси являє собою чистоту сахарози незнецукреної меляси, яка подається в сепаратор. Передбачається, що сепаратор досягне 93% чистоти екстракту та 92% виходу сахарози на основі стандартних цілей, і ця продуктивність гарантує вихід Z60 на рівні 81,6%. Однак передбачувана чистота екстракту меляси збільшується після додавання екстракту до другого відварювання. Зменшити чистоту меляси можна за допомогою відварювання утфелю останньої кристалізації, але для цього потрібна додаткова ємність вакуум-апарату чи зменшення швидкості переробки в продуктовому відділенні. Кольоровість білого цукру, показана в Таблиці 4, являє собою цукор, що утворюється під час кристалізації сиропу та екстракту. Дана модель передбачає, що за 330 днів роботи 97,6% сахарози в сиропі можна перетворити на білий цукор.
Переробка екстракту другого проходу на заводах з одним продуктовим відділенням
Аналогічно до переробки екстракту одного проходу, екстракт переробляється окремо після завершення виробництва сиропу. У цьому випадку екстракт меляси, що утворюється після кристалізації, спочатку зберігається і лише після цього направляється в сепаратор для виділення додаткової сахарози. Отриманий екстракт другого проходу переробляється окремо в продуктовому відділенні. Рекомендується повторно подати екстракт другого проходу на друге відварювання через високу кольоровість. Схема цього процесу з трьома відварюваннями показана на Графіку 7.
У Таблиці 5 показані результати відтворення цієї схеми переробки екстракту. Чистота кормової меляси знову являє собою мелясу, подану в сепаратор, що в цьому випадку є екстрактом меляси, виробленим під час першого проходу. Передбачається, що сепаратор досягне 91% чистоти екстракту та 89% виділення на основі виробничих даних другого проходу. Остаточний вихід Z60, включаючи перший та другий прохід, становить 87,5%. Однак, як і у випадку першого проходу, чистота меляси збільшується після додавання екстракту першого та другого проходу до другого відварювання. Знову можна мелясу подати до третього відварювання, щоб зменшити її чистоту, якщо вакуум-апарат має достатню потужність або якщо зменшити швидкість переробки в продуктовому відділенні. Загалом, після обох проходів 99,1% сахарози в сиропі можна перетворити на білий цукор.
Кольоровість білого цукру, показана в Таблиці 5, являє собою цукор, що утворюється в результаті кристалізації сиропу, екстракту першого проходу та екстракту другого проходу. Цукор, вироблений з екстракту другого проходу, має 74 IU, що вказує на те, що він може бути занадто темним, щоб стати кондиційним. Для зменшення кольоровості може знадобитися інтенсивне промивання для відварювання утфелю другої та останньої кристалізації, або можна змішати його з білим цукром безпосередньо перед його реалізацією.
Графік 7. Схема кристалізації з трьома відварюваннями для переробки екстракту другого проходу
Таблиця 5. Результати відтворення переробки екстракту другого проходу з одним продуктовим відділенням
Чистота кормової меляси (%) | Чистота сепараційного екстракту (%) | Виділення сепаратора (%) | Остаточний вихід Z60 (два проходи) (%) | Чистота екстракту меляси другого проходу (%) | Кольоровість білого цукру (IU) | Вихід цукру з сиропу (%) | ||
Сироп | Екстракт | Екстракт другого проходу | ||||||
72,2 | 91,0 | 89,0 | 87,5 | 69,0 | 20 | 30 | 74 | 99,1 |
Переробка екстракту одного проходу на заводах з продуктовим відділенням для екстракту
У цьому випадку екстракт можна переробити одночасно з сиропом, але кристалізація екстракту відбувається в окремому продуктовому відділення. Замість подачі екстракту до другого відварювання його можна додати до першого вакуум-апарату для стандартної технології трьох відварювань. Незважаючи на те, що вироблений цукор може мати високий рівень кольоровості, він надходить у клерувальний апарат, а потім до першого вакуум-апарату звичайного продуктового відділення, що забезпечує достатнє його знебарвлення. Екстракт меляси не переробляється під час другого проходу. Цей процес показано на Графіку 8.
У Таблиці 6 показані результати відтворення цієї схеми переробки екстракту. Передбачається, що сепаратор досягне 93% чистоти екстракту та 92% виділення, що гарантує Z60 на рівні 81,6%. У цьому випадку, так як екстракт можна додати до першого відварювання продуктового відділення для екстракту, чистота екстракту меляси зменшується, порівняно з попередніми схемами, і складає близько 60%. Оскільки білий цукор, вироблений в продуктовому відділенні екстракту, направляється через звичайне продуктове відділення для подальшого знебарвлення, то остаточний білий цукор як із сиропу, так і з екстракту, виробляється разом, і в Таблиці 6 показано лише один ступінь кольоровості. У цілому, 98,3% сахарози в сиропі можна перетворити на білий цукор.
Графік 8. Схема переробки екстракту одного проходу з продуктовим відділенням для екстракту
Таблиця 6. Результати відтворення переробки екстракту одного проходу з продуктовим відділенням для екстракту
Чистота кормової меляси (%) | Чистота сепараційного екстракту (%) | Виділення сепаратора (%) | Вихід Z60 (%) | Чистота екстракту меляси (%) | Кольоровість білого цукру (IU) | Вихід цукру з сиропу (%) |
61,6 | 93,0 | 92,0 | 81,6 | 61,6 | 18 | 98,3 |
Безкінечна переробка екстракту
У цій схемі кристалізації екстракт із сепаратора змішується з сиропом, а об'єднаний потік переробляється в однаковій конфігурації трьох відварювань. Частина потоку екстракту направляється до другого відварювання для контролю кольоровості білого цукру. Меляса, вироблена після кристалізації, направляється в сепаратор. Оскільки весь потік меляси направляється назад до установки дешугаризації (MDS), цей варіант називається "безкінечною" переробкою. Схема цього процесу показана на Графіку 9.
Безкінечна переробка є логістично простою, оскільки вона не потребує зберігання меляси або додаткової кристалізації. Однак, безкінечна переробка зменшує пропускну здатність сепаратора, і це може призвести до накопичення нецукрів, які важко піддаються видаленню за допомогою хроматографії. Ці нецукри можуть накопичуватися в мелясі і негативно впливати на показники роботи сепаратора. Крім того, переробка екстракту призводить до постійної зміни якості меляси, що ускладнює правильне та належне налаштування сепаратора.
Результати відтворення схеми безкінечної переробки екстракту наведені в Таблиці 7. Виходячи з виробничих даних, сепаратор передбачав досягнення 91% чистоти екстракту та 87,2% вихід сахарози, в результаті чого вихід Z60 склав 74,2%. В цілому, очікується, що безкінечна переробка екстракту дозволяє виділити 98,9% сахарози з сиропу для виробництва білого цукру.
Графік 9. Схема безкінечної переробки екстракту
Таблиця 7. Результати відтворення безкінечної переробки екстракту
Чистота кормової меляси (%) | Чистота сепараційного соку (%) | Виділення сепаратора (%) | Вихід Z60 (%) | Кольоровість білого цукру (IU) | Вихід цукру з сиропу (%) |
60,9 | 91,0 | 87,2 | 74,2 | 25 | 98,9 |